
The key roles for Six Sigma implementation include:
#SIGMA DEFINITION HOW TO#
In this case, the Six Sigma focus looks at proactively eliminating the defect, while a non-Six Sigma approach simply reacts to the problem without identifying the cause.įor a closer look at where to apply Six Sigma, see “ How to find the perfect project for Six Sigma success.”Ī key concept in Six Sigma is the idea of establishing clear leadership roles and a hierarchy for quality management. A Six Sigma solution would be to “investigate and control key inputs that contribute” to defective parts coming from Station 20 to keep it from happening again in the future. ISixSigma offers the example of a “slow cycle time at Station 30” due to defective parts coming from “Station 20.” A “non-Six Sigma solution” would attempt to rebalance the assembly line, while re-doing the work, keeping cycle time low and not spending on labor. Project needs to be approached with knowledge of variations in process inputs and how to control and eliminate defects.

Focus on reducing “operation variation” to make it easier for untrained operators.Don’t go into the project with a pre-determined solution - that means you already know the fix.Each project needs to have a clear process of inputs and outputs.

To find projects in your organization that would benefit from Six Sigma they need to fit some criteria: When a business needs to develop a product or process that doesn’t already exist or when a product has been optimized but still falls short, that’s when you want to use DMADV. The DMAIC methodology is designed for existing process or products that aren’t meeting customers’ needs or performing to standards. The DMAIC and DMADV methodologies seem similar, but they have different use cases.

Verify that the final iteration of the product or process is approved by all customers and clients - whether internal or external.Design the process at a high level before moving onto a more detailed version that will become the prototype to identify errors and make modifications.Analyze multiple options and alternatives for the customer along with the estimated total life cycle of the project.Measure and identify the customer’s critical to quality (CTQ) requirements and translate them into clear project goals.Define realistic goals that suit the customer’s requirements or the business strategy.
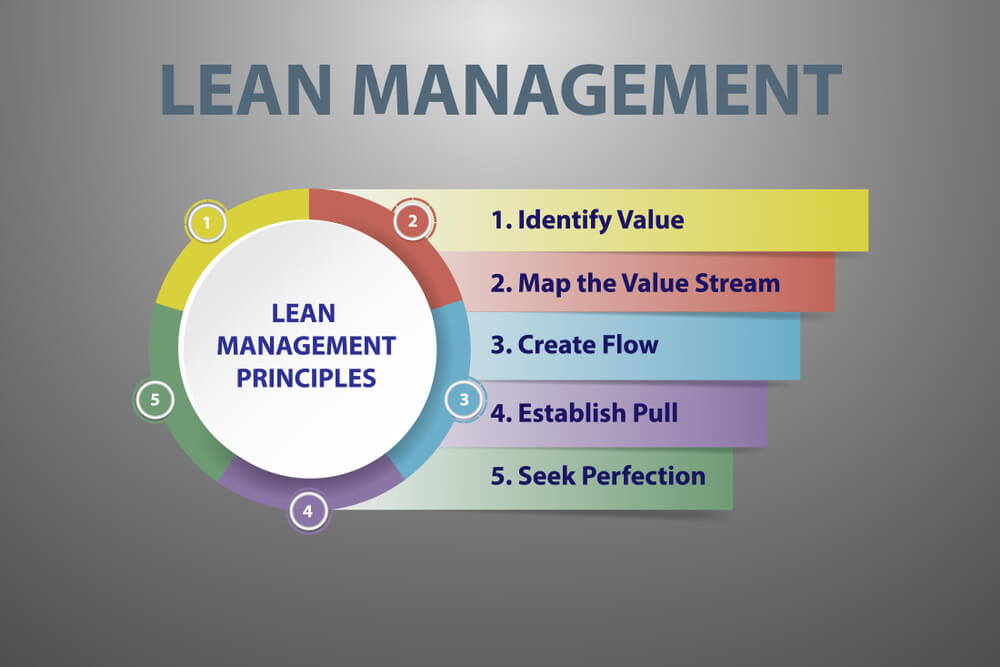
The Six Sigma DMADV, also known as the Design For Six Sigma (DFSS), includes five stages:
